Concluding a further phase of repair and reconstruction in May 2019, the Iron Gate I (Đerdap I) power station ramped up power generation in a newly waterproof facility. The Penetron System was specified as the more comprehensive solution over a competitive product.
When it was first completed in 1972, the Iron Gate I Hydroelectric Power Station had 12 turbines generating 2,052 MW, making it one of the largest hydroelectric power stations in the world. Located in the Iron Gate Gorge, which forms the border between Serbia and Romania, it is the largest dam on the Danube River. It is operated as a joint venture between Serbia and Romania. Both countries share the power generated by the dam, each maintaining their own power station facility. Renovations and upgrades to the Serbian power station have been ongoing since 2008.
“The Iron Gate facility is an old development, but remains a point of pride for Serbian industry,” says Theodor Mentzikofakis, Managing Director of Penetron Hellas. “Because of the importance of the facility and the age of the power station infrastructure, repairs to the concrete elements are being carried out on a systematic and ongoing basis.”
Choosing a Durable Repair System
When the project engineer looked to specify a waterproofing solution, a local distributor of a competitive crystalline product was initially considered. However, because of the wide range of repairs and reconstruction needed by the Electric Company of Serbia and LEVER Engineering, the Penetron System of products was chosen as the preferred solution: it provides a complete solution with the required technical assistance to ensure a successful repair.
The deterioration in the power station’s concrete structure needed to be repaired with an injection system. The Penetron Hellas team was invited to the Iron Gate I facility in early 2019 by Lever Engineering, the contractor in charge of repairs and renovation, to train the contractor teams how to properly apply PENETRON INJECT. This advanced crystalline-based grout is manually injected into a concrete matrix to fill out and seal deeply embedded voids, cracks and fissures.
The initial applications of PENETRON INJECT were done by Lever Engineering. Currently, the technical team responsible for the maintenance of the water dam and power plant is undergoing training. Once completed, the team will continue with the repairs as further compromised concrete surfaces are identified.
Working from the Inside Out
“We showed the technical team how PENETRON INJECT is effective when filling hollow spots and voids often encountered in older concrete structures. It quickly adds stability and strength to repaired areas,” adds Theodor Mentzikofakis. “With its water-like viscosity and the extremely fine particle size of the ingredients, PENETRON INJECT efficiently penetrates into very fine hairline cracks, pores and capillaries to displace any water present in the concrete and permanently seal the matrix with an insoluble crystalline structure.”
All future repair and waterproofing treatments at the Iron Gate I power station’s concrete structures will be completed with a combination of PENETRON, PENECRETE MORTAR and PENEPLUG. In the most recent phase, PENETRON crystalline material was topically applied to the concrete surfaces in the power plant’s facility building. The plant’s two water reservoirs were first repaired with PENECRETE MORTAR and PENEPLUG, before a final coat of PENETRON slurry is applied. PENECRETE MORTAR and PENEPLUG are also being used for ongoing repairs of the facility’s retaining walls.
“The power plant requires continuous repairs due to the age of the facility,” adds Theodor Mentzikofakis. “Fortunately, the Penetron System ensures an increase in durability, increasing the service life of the Iron Gate I facility.”
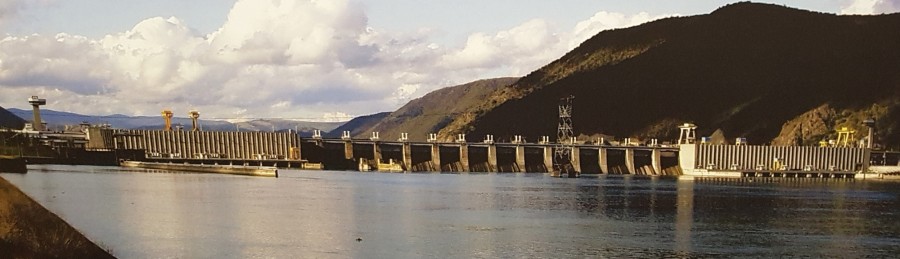
Fixer-upper: Built in 1972, the Iron Gate I Power Station was one of the world’s largest hydroelectric power stations. Recently, the deteriorated concrete structures underwent a complete renovation.
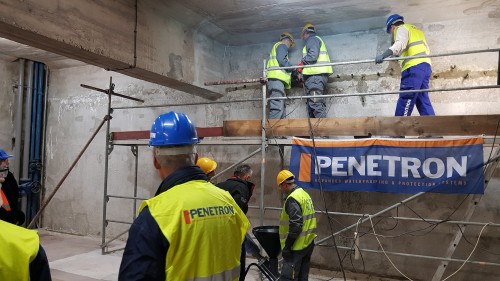
Rejuvenation treatment: PENETRON INJECT, a crystalline-based grout, was injected into the Iron Gate I Power Station’s concrete matrix to fill out and seal deeply embedded voids, cracks and fissures.